When Blickfeld was founded in 2017, LiDAR sensors were bulky, maintenance-intensive and very expensive to produce. Blickfeld’s founders set out to change that: They developed a LiDAR sensor with a simplified set-up, always keeping scalability in manufacturing in mind.
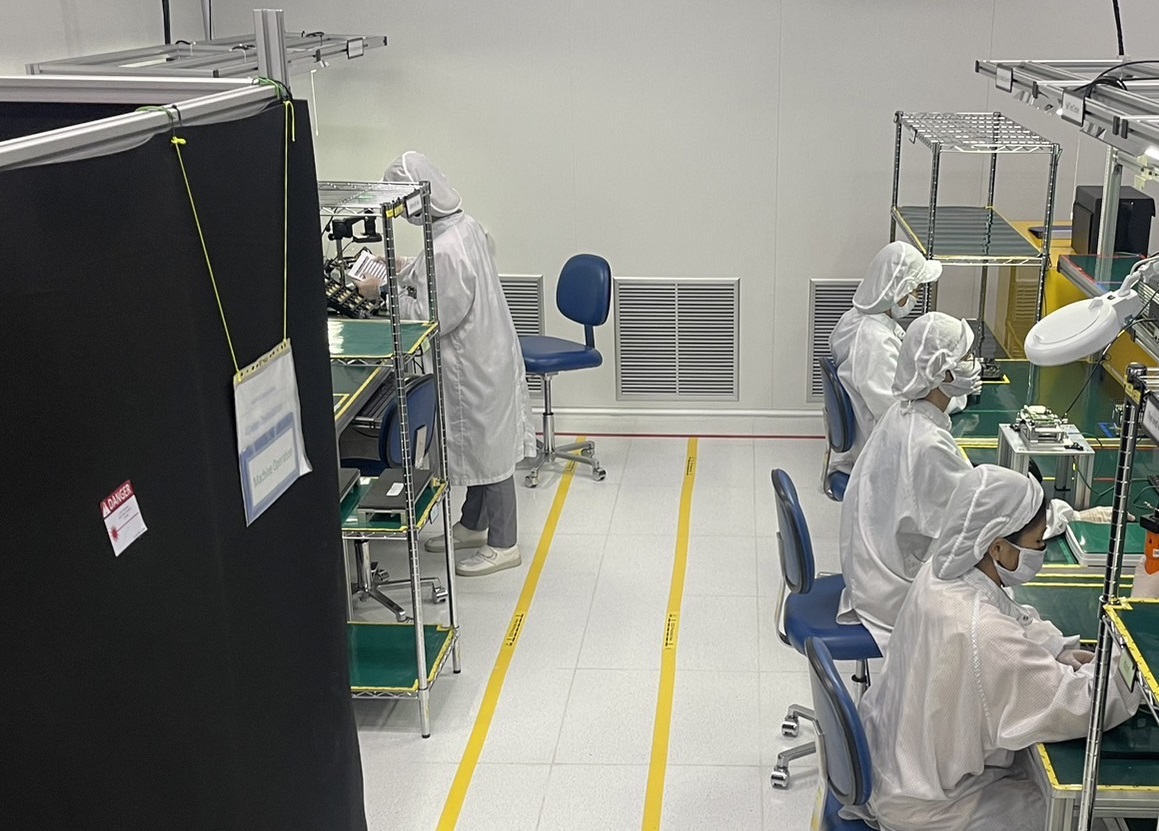
The Blickfeld technology relies on a single laser source and MEMS mirrors that deflect the laser beam onto the surroundings, thus creating the field of view. One of the many advantages of this technology is that the production of the sensors can be easily industrialized.
Our production partner, Fabrinet, supports us in achieving cost-effective and high-volume production of the latest Blickfeld sensor, Qb2, while meeting the highest industrial quality requirements. We chose Fabrinet as production partner after a careful selection process which included the development of various manufacturing concepts as well as VDA audits to evaluate the partner’s capabilities, management systems, and more.
Industrialization project culminates in start of production
The industrialization of Qb2 was a massive project which spanned over 28 months and involved a team of close to 100 people at Blickfeld and Fabrinet. Important milestones along the way were the ISO 7 cleanroom setup at the Fabrinet production facility along with the completion of the production line and the delivery of the first samples. We are now extremely happy to announce the start of mass production in May 2023!
To get there, thorough planning and strong project management were crucial. Preventive methodologies such as Failure Mode and Effects Analysis (FMEA) and risk analysis were implemented, the stability of each manufacturing step was ensured and design studies involving materials, adhesives, and manufacturing processes were performed.
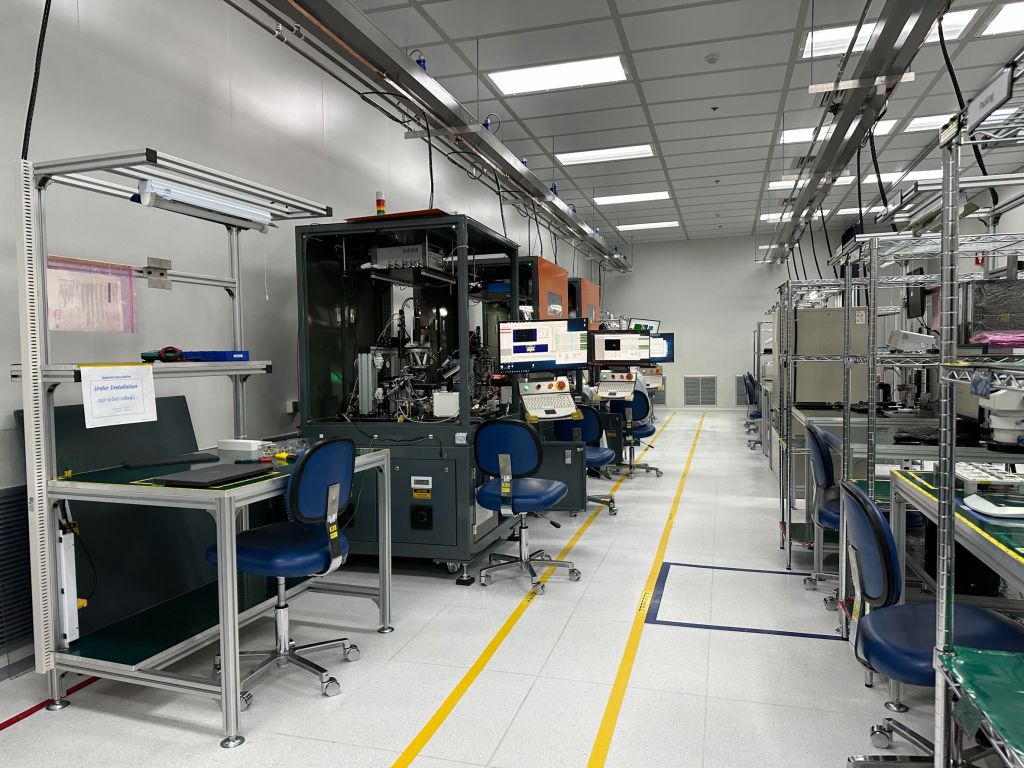
While the core of our sensors, the Beam Deflection Unit (BDU), is still produced in Munich by Blickfeld experts, Fabrinet handles all other aspects, including the production of the Laser Detector Module (LDM), the Qb2 assembly, and testing. Testing encompasses design quality, production quality, and end-of-line testing. In total, each sensor undergoes more than 140 tests before it is delivered to customers.
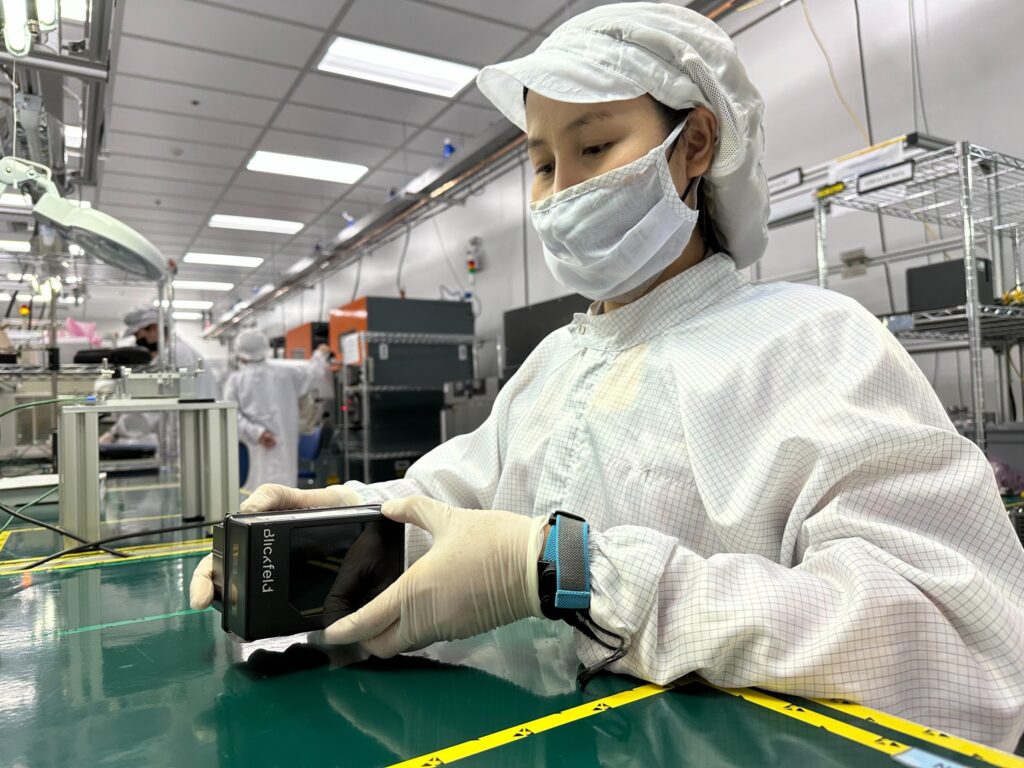
The industrialization of Qb2 is an important step for Blickfeld
Terje Noevig, Blickfeld’s COO explains: “With the first generation of our sensors, the Cube, we demonstrated the viability of our technological approach and the ability to produce in series. Qb2 represents a significant leap forward in terms of cost, performance, quality, features, and quantity. It has been developed from scratch to meet industrial requirements, with an annual production capacity reaching very high five-digit numbers. We are extremely excited about reaching SOP and to get started on those numbers!”