Bulk Solids Measurement with 3D LiDAR
Accurate Silo Fill Level Monitoring
Accurate, contactless, and real-time
Monitoring the fill level of silos storing bulk solids is essential for accurate inventory management, timely replenishment, and efficient operations. Traditional level sensors often struggle with irregular surfaces, dusty environments, or cone-shaped fill patterns. Blickfeld’s 3D LiDAR solution provides high-resolution, spatially accurate volume data, helping you reduce overfilling risks and avoid unexpected shortages. This advanced approach to bulk solids measurement enables more reliable and efficient processes across various industries.
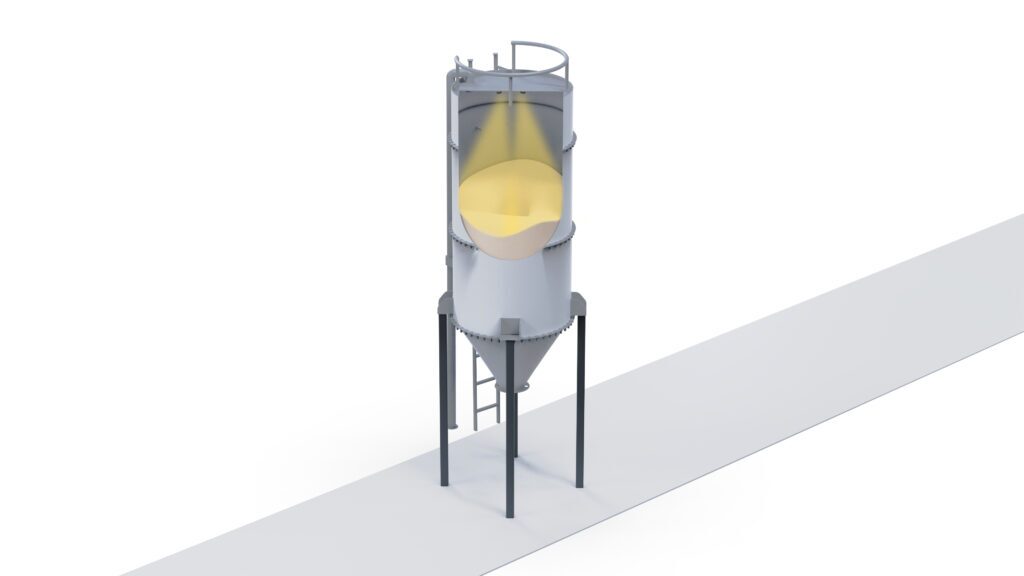
Real-Time Inventory Insights
Monitor stock levels continuously to improve planning and ensure timely replenishment.
Enhanced Operational Safety
Eliminate manual silo inspections and reduce the risk of accidents.
Reliable Overfill Prevention
Avoid spillage and material loss with accurate, uninterrupted volume data.
Seamless System Integration
Connect volume data to your existing ERP or SCADA systems for full process transparency.
How It Works
Blickfeld’s 3D LiDAR sensors scan the full surface of the stored material in silos or bunkers. The system creates a complete 3D model of the fill level, regardless of material shape, consistency, or layout. Volume is calculated automatically and continuously—no manual checks or recalibration required.
Our software supports cone-shaped zone definitions and applies interpolation and extrapolation where parts of the pile are temporarily hidden, ensuring consistent results even in complex conditions. The system delivers highly accurate LiDAR level measurement with minimal effort.
This detailed spatial data allows the system to calculate the exact volume of bulk material on the vehicle—whether the load is uneven, loosely packed, or variable in moisture.
Unlike weight-based systems, which can be inaccurate with wet or fluffy materials, the LiDAR-based approach provides consistent, contactless truck bed volume measurement with no manual input required. The result is dependable data for billing, inventory tracking, and regulatory compliance.
How 3D LiDAR Compares to Traditional Silo Measurement Methods
When it comes to monitoring bulk solid levels, traditional sensors like ultrasonic, radar, or mechanical systems often struggle with dust, buildup, or irregular surfaces. 3D LiDAR covers the full surface, not just a point, so you get a true picture of your inventory, not an estimate.
Technology | How It Works | Advantages | Common Limitations |
---|---|---|---|
Ultrasonic Sensors | Use sound waves to detect surface distance | Simple and low-cost | Sensitive to dust, noise, and sloped surfaces |
Radar Sensors | Emit microwave signals for level detection | Works in dusty and harsh environments | Measure only one point; may miss irregular fill shapes |
Capacitance Probes | Detect changes in electrical properties when in contact | Reliable for small containers | Intrusive; affected by buildup or bridging |
Mechanical Systems | Use paddles or weights to detect material levels | Simple concept; can trigger basic alarms | Require maintenance; slow and wear-prone |
Load Cells | Estimate weight of the entire silo | Continuous weight monitoring | Indirect volume measurement; no shape or surface detail |
LiDAR Sensors | Emit laser pulses to create a 3D map of the surface | Non-contact, accurate 3D volume measurement, handles irregular surfaces well | May require line-of-sight and protection in harsh environments |
From open stockpiles to silos and truck beds, bulk materials are stored in many ways. LiDAR technology enables accurate, real-time volume monitoring across all these storage types, helping businesses optimize operations and reduce manual effort.
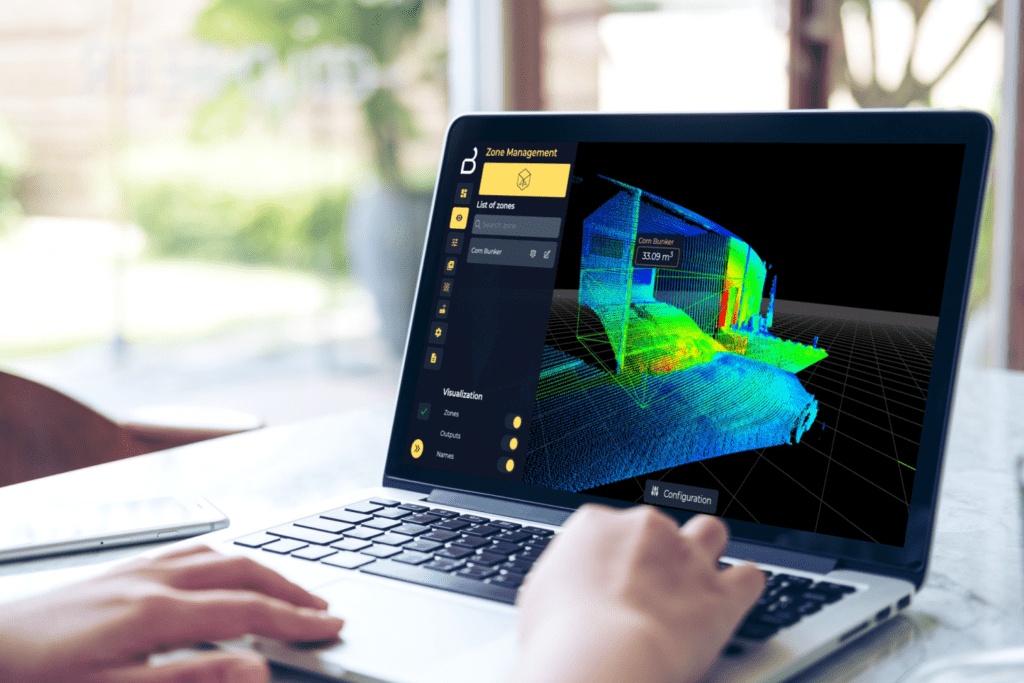
Scalable All-in-One Solution
Complete Scalable Solution
Blickfeld offers more than just sensors: we deliver a complete, scalable solution tailored to your storage environment. Our compact LiDAR devices can be mounted on silo roofs or existing frames and adapted to a wide range of silo types, from vertical silos to large open bunkers. For larger storage areas, multiple sensors can be combined for full 3D coverage. Our experts support you in designing the optimal setup, ensuring accurate results and minimal blind spots from the start.
Service, Support & Integration
From the first feasibility study to long-term operation, we support you at every step. Our consulting services help assess environmental conditions, mounting options, and data architecture. Remote commissioning makes deployment quick and efficient, while our tiered support ensures fast assistance, whether via remote access or site visits.
We also offer tailored pilot programs, giving you the opportunity to test the system in your specific environment before full deployment. Real-time silo monitoring data is available through local dashboards or secure remote interfaces, ready to integrate into your existing ERP or SCADA systems.
Supported Materials and Storage Types
Our solution handles a wide range of bulk solids typically stored in silos, such as grains, animal feed, cement, and plastic pellets. It is tailored for industries like agriculture, manufacturing, and construction, providing precise and reliable level monitoring for enclosed and open storage.
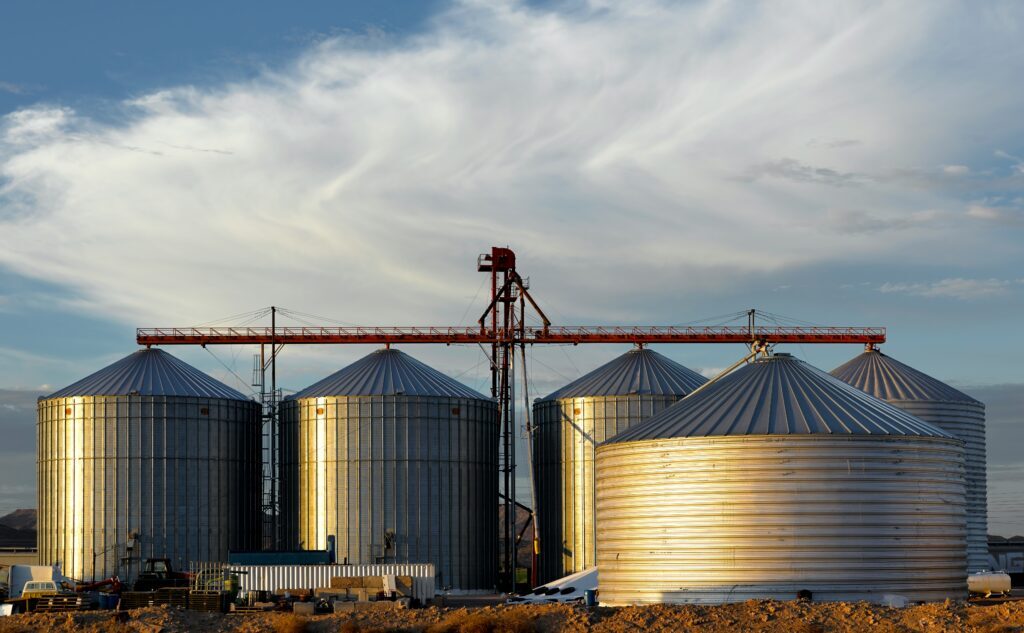
Key Features
✔ Continuous, contactless volume monitoring of silos and bunkers
✔ Accurate fill level tracking with full 3D surface data
✔ Real-time access via dashboard or remote interface
✔ Cone zone support with interpolation/extrapolation of occluded areas infrastructure
✔ Compact, industrial-grade design with easy setup
Key Technical Data
Measurement Range & Coverage
Typical application range: 1–100 meters. With a field of view of 90° × 50°, the sensor captures broad surface areas even in large or irregularly shaped silos.
Coverage depends on mounting height and tilt angle—e.g., from approx. 15 × 12 m at 3 m height to 56 × 45 m at 20 m height.
Detailed coverage examples available on request.
Accuracy & Resolution
High-resolution 3D scanning with up to 2,400 vertical scan lines per frame and configurable horizontal resolution down to 0.25°. Narrow laser beam divergence (0.25° × 0.25°) ensures precise surface detection for accurate level and volume measurement.
Sensor Mounting Height & Installation Requirements
Typical mounting height: 3–20 meters, depending on silo size. Ensure a stable base, clear field of view, and at least 20 cm clearance around the heatsink.
Single or multi-sensor setups may be used based on coverage needs.
CAD data available at https://www.blickfeld.com/resources/.
Data Access & Integration
Access measurement data via online or offline dashboards. Standard API available for system integration. Support provided for ERP, SCADA, or custom data interfaces.
Environmental Protection & Safety
IP67-rated housing, Class 1 eye-safe laser (IEC 60825-1). CE, FCC, RoHS compliant; TAA-compliant version available.
Contact us to ask about ATEX options.
Get in Touch
Would you like to learn more about silo fill level monitoring with Blickfeld’s 3D LiDAR technology?
Whether you’re looking to automate measurements, improve accuracy, or optimize inventory management—send us a message, give us a call, or schedule a meeting. We’re happy to support you!
Contact Form
Contact our Sales Team

Akram Ben Youssef
Junior Sales Manager
Region: Europe
+49 89 230 69 35 60
Schedule a meeting
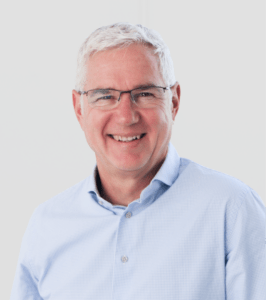
Dirk Rathsack
VP Business Development & Sales
Region: Rest of World
+ 49 174 230 3357
Schedule a meeting
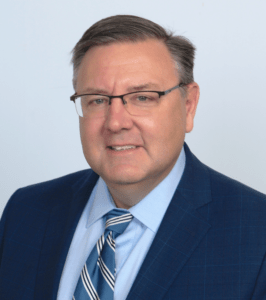
Patrick Pylypuik
President, Blickfeld North America Inc.
Region: North America
+1 (855) 335 4327