In the past, LiDAR systems struggled with a number of problems: they were lacking in efficiency and robustness for use in the automotive industry. An even bigger problem was the cost of a LiDAR system: The sensors were far too expensive for the automotive mass market. Blickfeld tackles this problem and developed LiDAR sensors for the mass market. The Munich-based start-up’s technology relies on MEMS silicon components and highly automated production – and is paving the way for autonomous vehicles.
The problem: lack of robustness and high production costs
LiDAR technology is not a new invention; it has been used in various applications, such as measuring emissions in atmospheric research or remote sensing in archaeology since the 1960s. However, LiDAR systems have faced some serious problems until now:
- LiDAR systems are very large.
- The mechanics used are sensitive to harsh environmental conditions such as vibrations, heat and cold.
- The range of previous LiDAR systems is not sufficient for many applications.
- And: LiDAR sensors today are neither available in large quantities nor at affordable prices.
All these points pose major problems for the automotive industry in particular, which is desperately looking for high-performance LiDAR systems with a robust and production-scaleable design. Why? Because LiDAR is essential for the autonomous cars of tomorrow. Mobility is about distances and speeds. Not-colliding is essential in road traffic – LiDAR sensors detect immediately and reliably. Experts therefore predict that several LiDAR sensors per car will be needed in the future. However, to achieve this, the problems mentioned must be overcome.
What is the root of those problems?
Classical mechanically rotating LiDAR concepts are fragile and complex in design and production, resulting in large dimensions and high prices. Although other technologies and designs such as optical phased array and flash LiDAR have the potential to significantly reduce LiDARs in size and cost, they are still at the beginning of development or have system-related disadvantages, such as a very limited range.
The solution: MEMS-based LiDAR sensors for the mass market
LiDAR sensors based on MEMS mirrors are a promising solution. Their silicon construction is already well advanced and implemented very successfully in many automotive applications. In addition, MEMS technology does not require rotating components and is therefore much more robust and durable than mechanical LiDAR systems. MEMS mirrors available on the market today have small mirror sizes and small deflection angles, as these were sufficient for their previous use. Their performance in terms of range and field of view is therefore limited.
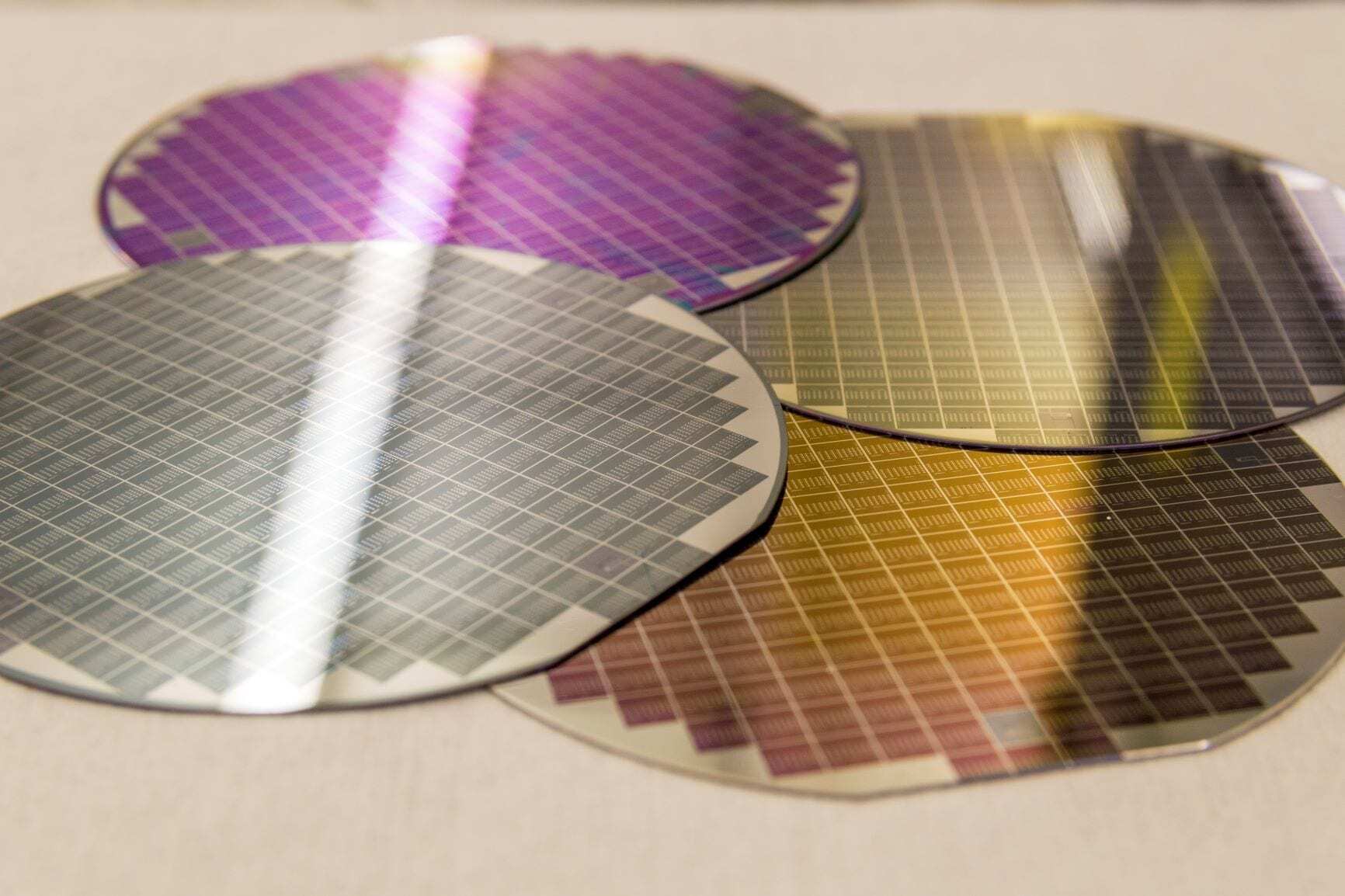
The Blickfeld solution: Particularly large mirrors
Blickfeld’s LiDAR system relies on MEMS. But how does their system differ from other MEMS based LiDARs? To extend the range of the sensors, Blickfeld has developed its own MEMS mirrors. With generous dimensions of more than 10 millimeters mirror diameter, a high proportion of incident light can be directed onto the photodetector. Thus, the LiDAR reliably detects even weakly reflecting objects at a distance of more than 180 meters. In comparison, conventional MEMS mirrors have diameters of only a few millimetres and small deflection angles, which reduces the range and field of view accordingly when used in LiDARs.
Further advantages of the MEMS mirror used in Blickfeld products are:
- a large deflection, which enables a scanning angle of approx. 100° x 30° and thus a wide field of view.
- Spatial filter effect due to coaxial design: The light emitted by the laser and deflected onto the scene by the MEMS mirror is reflected by the objects in the field and returned to the detector along an optically almost identical path. This means that light photons are only collected from the exact direction in which the laser sent them. This minimizes the background light, for example from the sun or other LiDARs, and produces a very high signal-to-noise ratio, which benefits the range.
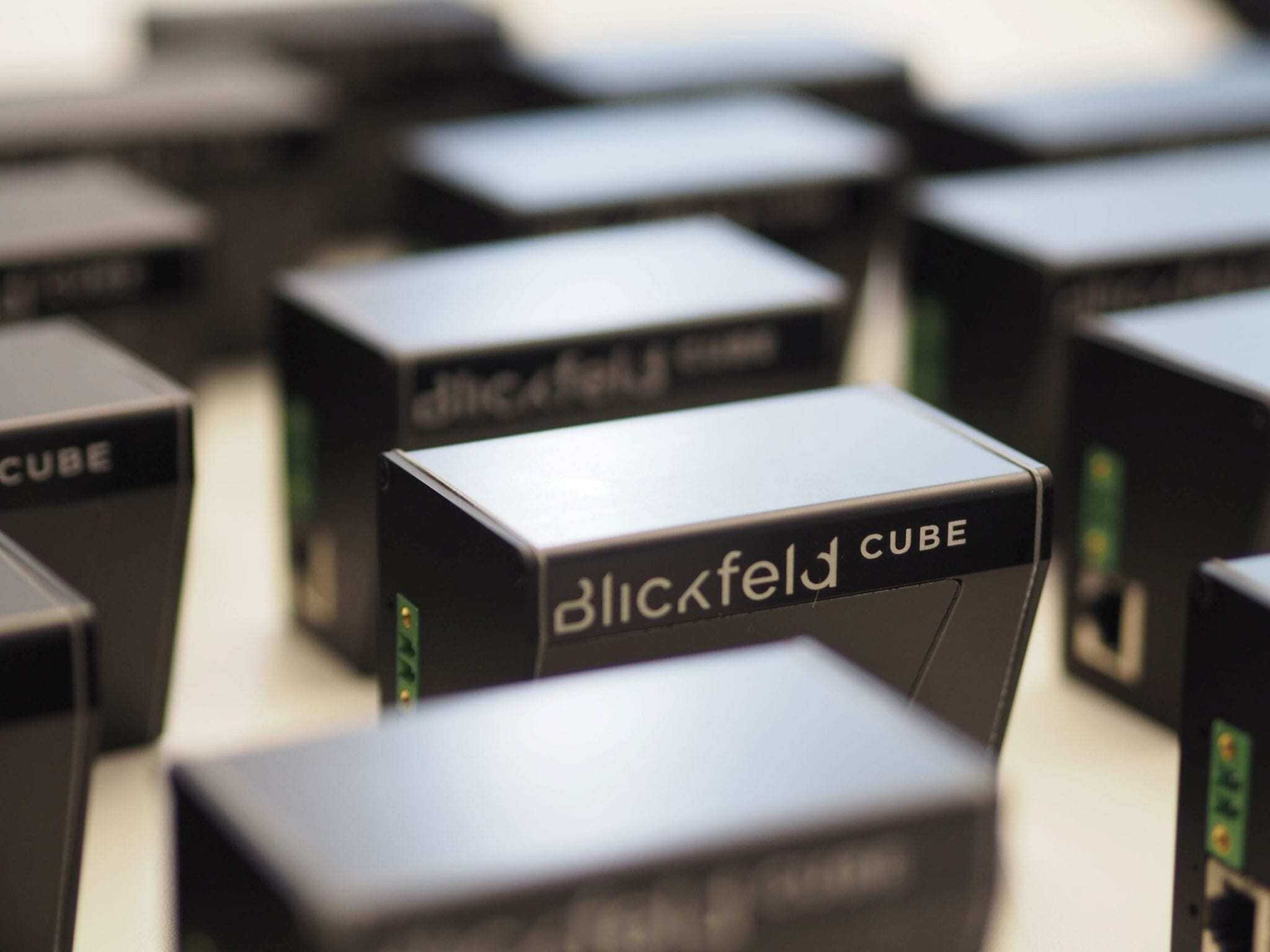
How does Blickfeld address the problem of production?
The MEMS mirrors developed by Blickfeld solve three of the four problems mentioned above: The company’s LiDARs are space-saving, robust and performant. But how does Blickfeld tackle the problem of cost-intensive production? By manufacturing the mirrors with low-cost photolithographic production techniques that allow highest precision with extreme scalability, so-called MEMS silicon manufacturing. A standard silicon wafer with a diameter of 200 millimeters is turned into hundreds of highly automated MEMS components simultaneously. This method, which has been tried and tested in the semiconductor industry for decades, enables the technology to conquer the mass market.
The MEMS mirror is embedded in a ‘commercial off-the-shelf’ structure, i.e. commercially available standard components. These laser and detector units, that are available on the market, enable a cost-effective and scalable production of the sensors.
Autonomous vehicles and so much more
The use of LiDAR sensors extends far beyond the automotive industry and the fields of application are versatile. In order to take advantage of the technology, Blickfeld has eliminated the major problems of LiDAR systems and has made them accessible to the mass market. The LiDAR era has only just begun!